Understanding Chinese-English Motor Labels A Guide to Common Manufacturing Text Patterns
Understanding Chinese-English Motor Labels A Guide to Common Manufacturing Text Patterns - Motor Efficiency Markings From Numbers to Real Performance
Motor efficiency markings aren't just numbers; they reveal how well a motor actually performs and how economically it operates. These markings, often found on the motor's nameplate, include key details like the nominal full-load efficiency and the motor's capabilities at different voltages and horsepowers. This information is crucial for getting the most out of your motor. We see a growing trend toward stricter efficiency standards like the Grade IE2 requirement in China, reflecting a global shift towards more energy-efficient technologies. It's important to understand that higher efficiency ratings translate to tangible benefits. They can lower operating temperatures and potentially extend the lifespan of the motor, resulting in reduced operating costs over time. This highlights the importance of paying close attention to motor efficiency ratings when making purchase decisions, especially considering the increased focus on energy efficiency across various industries. While manufacturers often provide these ratings, understanding their implications for your specific application is essential for optimal motor selection and operation.
1. While motor efficiency is often presented as a simple numerical value, understanding its practical implications requires caution. A higher efficiency number doesn't guarantee superior performance across all applications, making it crucial for engineers to consider the specific operational context.
2. It's essential to recognize that motor nameplate efficiency often represents just the motor itself. This can create a disconnect between the labeled value and the actual system efficiency, especially when auxiliary components like gearboxes or belts introduce additional losses.
3. The methods used to test and determine motor efficiency can vary significantly among manufacturers. This lack of standardization makes direct comparisons between motors from different sources challenging and highlights the need for universally accepted testing procedures.
4. The materials used in motor construction significantly impact performance. For instance, the choice of winding wire and core materials can influence heat generation and power losses, ultimately affecting the achieved efficiency compared to the labeled value.
5. Motor efficiency labels often emphasize full-load conditions. However, many applications involve variable loads, where motors may exhibit quite different efficiency characteristics. This difference is a crucial consideration for engineers when designing systems with fluctuating load demands.
6. Efficiency calculations frequently don't fully account for the influence of temperature. As motors operate, their internal temperature rises, leading to increased resistance and decreased efficiency. This phenomenon is often not reflected in the initial efficiency markings.
7. Environmental factors can influence a motor's efficiency in ways not usually captured by standard ratings. Factors like humidity and altitude can subtly affect performance, though they are rarely incorporated into typical efficiency labeling.
8. Motor efficiency isn't static. Over time, components wear down, particularly in applications with frequent on/off cycles, leading to gradual performance degradation. The initial efficiency rating may not reflect these long-term changes.
9. Recent innovations in motor technology, like the rise of permanent magnet synchronous motors, pose a challenge to traditional efficiency standards. This suggests that the current efficiency labeling practices might need updates to accurately reflect the capabilities of newer motor designs.
10. Label-based assessments of motor performance can sometimes be misleading. Rigorous real-world testing is crucial for understanding the actual performance under specific operating conditions, highlighting the importance of comprehensive evaluation beyond simply relying on the provided efficiency metrics.
Understanding Chinese-English Motor Labels A Guide to Common Manufacturing Text Patterns - Frame Size Standards What NEMA Numbers Actually Mean
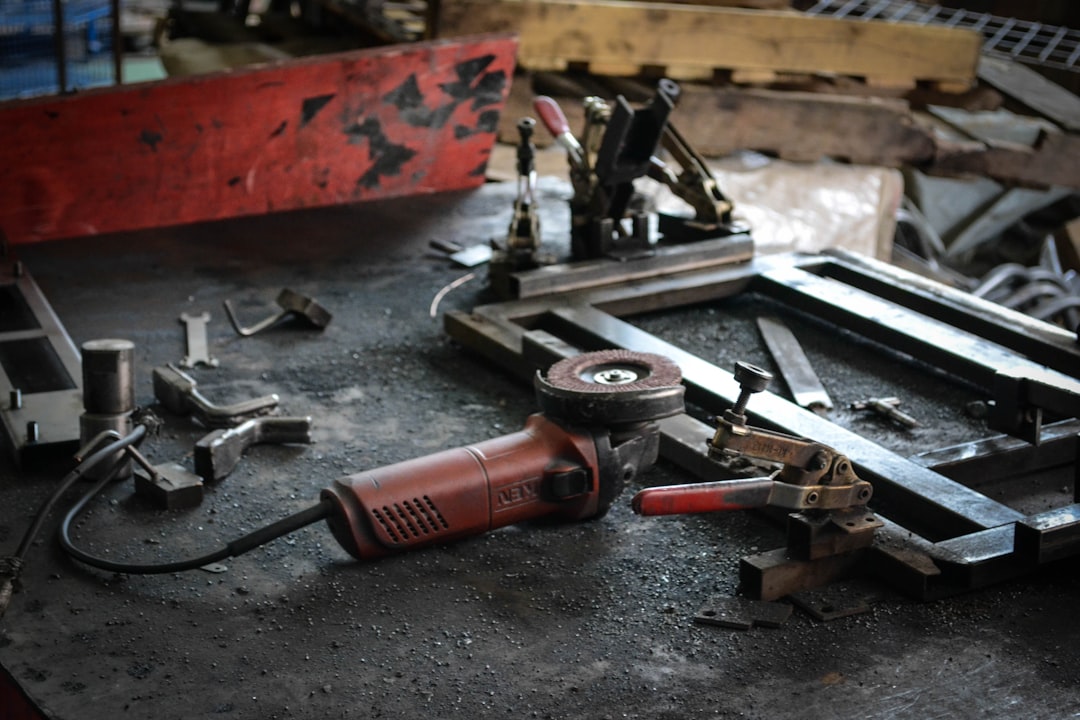
NEMA frame size standards primarily focus on the physical dimensions of motors, specifically the distance from the base to the shaft's center, often referred to as the "D" dimension. This standard uses a numerical system where the first two digits, when divided by four, directly translate into the shaft height in inches. For instance, a NEMA 324T motor has an 8-inch shaft height (32 divided by 4). While these standards are relatively easy to interpret, it's important to realize that they only address mounting points and do not include information about the motor's overall body diameter. This means accurately interpreting suffixes and other designations is essential for correctly selecting replacement motors or ensuring proper fit within a system. The fact that NEMA frame sizes solely concern mounting aspects reveals a subtle complexity in motor selection, highlighting the importance of detailed understanding when navigating a wide range of motor options. Ultimately, while NEMA simplifies some aspects of motor selection, deeper knowledge is still needed for optimized applications.
1. NEMA frame numbers, primarily used in North America, are a system for classifying electric motors based on their physical dimensions and how they are mounted. This standardized approach simplifies motor selection for a variety of applications.
2. A NEMA number signifies more than just the frame size. It also links to specific performance aspects, like the pattern for bolt holes and the shaft diameter. This ensures components within an electro-mechanical system can fit together correctly.
3. It's interesting that the NEMA system acknowledges different motor duty cycles, such as continuous or intermittent operation. This impacts how a motor functions under varying loads and guides engineers in choosing appropriate applications.
4. A unique feature of NEMA standards is their inclusion of efficiency ratings that are tied to the frame size, not just physical attributes. Engineers can thus assess both the motor's fit and anticipated performance using just the frame size number.
5. Unfortunately, frame sizes can differ between manufacturers. This can cause issues during procurement if engineers don't check compatibility carefully. It's crucial to confirm that the motor adheres to the intended NEMA standards to avoid design errors.
6. NEMA numbers also relate to horsepower ratings within a particular frame size. This means a larger frame usually supports a higher horsepower output without overheating, a vital consideration during motor selection.
7. It's somewhat surprising that the NEMA standard doesn't address inverter duty specifications. This is a challenge given the rise of variable speed drives in modern applications. Engineers must carefully consider if a motor is suitable for these types of systems.
8. NEMA also defines a category for premium efficiency motors, designed to operate at a lower cost while offering enhanced performance. This challenges engineers to think about the motor's life-cycle cost, not just the initial purchase price.
9. The standards have been updated over time to accommodate technological advancements and energy efficiency regulations. However, older installations with older frame sizes might not meet modern efficiency standards, highlighting the need for assessments during equipment upgrades.
10. It's important to realize that NEMA frame sizes can have a wide range of weights. For instance, a NEMA 48 frame motor can be twice as heavy as a smaller NEMA 143 frame. This significantly impacts the design and structural needs of the machinery that the motors power.
Understanding Chinese-English Motor Labels A Guide to Common Manufacturing Text Patterns - Converting Between Horsepower and Kilowatt Labels
When interpreting motor labels, especially those with Chinese-English text, it's crucial to be able to translate between horsepower (HP) and kilowatt (kW) power ratings. These are both units of power, and understanding their relationship is vital for matching a motor to a specific application. One horsepower is roughly equal to 0.746 kilowatts, while one kilowatt equals approximately 1.341 horsepower. You can easily convert between these units using simple formulas: kW = HP × 0.746 or HP = kW × 1.341. However, there's a catch. The term "horsepower" can have several different meanings, such as mechanical horsepower, electrical horsepower, and metric horsepower. These variations stem from different measurement standards and can be confusing if not properly accounted for. Understanding these conversion factors is essential, and awareness of the influence of service factors and motor duty cycles adds another layer of complexity. It's important to be mindful of these details to optimize motor selection and ensure long-term, reliable performance.
Horsepower (HP) and kilowatts (kW) are both units of power, but their origins are rooted in different measurement systems. Horsepower, developed within the imperial system, emerged from the world of steam engines. Kilowatts, on the other hand, are part of the metric system, reflecting a larger trend towards a more globally consistent scientific measurement approach.
The relationship between horsepower and kilowatts isn't immediately obvious. One horsepower is roughly equal to 0.7457 kilowatts. This conversion factor underlines the importance of correctly applying conversion formulas when interpreting motor labels, especially when working with diverse equipment and systems across different parts of the world.
In the realm of electric motors, it's noteworthy that kilowatts tend to be the preferred unit in specifications globally, while horsepower remains common in North America. This duality necessitates thorough attention to ensure motors are correctly applied in design and engineering, especially when working on projects that may involve equipment from various origins.
The term "mechanical horsepower" specifically refers to 1 horsepower as 745.7 watts, whereas "metric horsepower" is about 735.5 watts. This illustrates that even seemingly simple terms can be nuanced and can vary depending on the context in which they're being used.
Adding to the complexity, engine power ratings sometimes include "brake horsepower" (BHP), which is the engine's output measured at the crankshaft, isolated from other components or systems. This adds an extra layer of complexity when trying to compare it to kilowatt measurements, which usually reflect the motor's overall efficiency.
There have been differing standards for horsepower units throughout history, including metric and imperial definitions. This can lead to misunderstandings and discrepancies when comparing motors internationally. Engineers should be cognizant of these naming convention variations.
Horsepower itself has an interesting historical context. James Watt's ingenious marketing campaign convinced potential steam engine buyers they could better understand the power output by visualizing it in terms of horses. This clever bit of branding firmly established the term into common engineering vocabulary.
Conversions between horsepower and kilowatts demand precision, particularly in the world of mechanical design and applications. Incorrect conversions can result in underperformance or, potentially, overloading of equipment, making accurate conversion paramount for safe and efficient operations.
It's worth noting that as motor technology evolves, the methods of measuring power output are also changing. For example, the rise of advanced, high-efficiency motors could require updated conversion considerations to account for potential performance variances between different motor types.
Lastly, because electrical standards vary around the globe, a good understanding of how to convert horsepower to kilowatt ratings is crucial when procuring motors from international manufacturers. This is necessary to ensure the motor will properly integrate with existing equipment and systems in any given engineering project.
Understanding Chinese-English Motor Labels A Guide to Common Manufacturing Text Patterns - Duty Cycle Labels Understanding Operating Time Limits
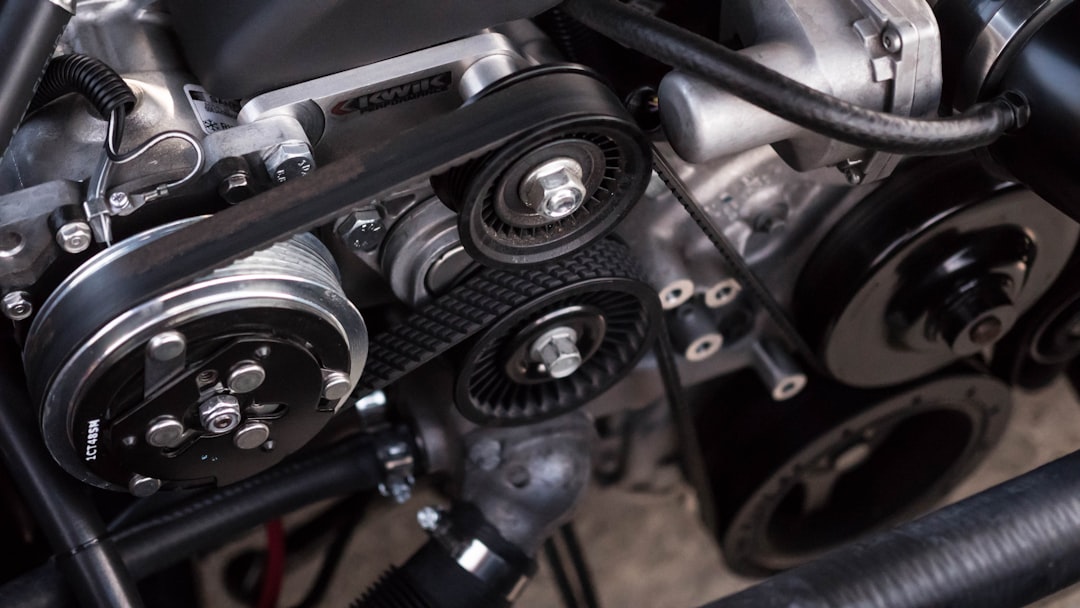
Duty cycle labels provide vital information about a motor's operating time limits, helping ensure its proper use and extended lifespan. These labels, classified under standards like IEC 60034, categorize motor operating conditions. Common categories include continuous duty (S1), where the motor operates continuously until reaching thermal equilibrium, short-time duty (S2), with operation limited to durations too short for thermal equilibrium, and intermittent duty (S3), involving periods of operation interspersed with breaks for cooling. Choosing the correct duty cycle is not only about achieving desired performance but also about optimizing cost. Improperly matched duty cycles can lead to motor overheating and reduced lifespan. The interplay of duty cycles, temperature rise, and efficiency is crucial for correct motor selection. This is especially true for applications with specific operational demands, such as printing, where the motor must manage varying loads effectively. For both engineers and technicians, understanding how duty cycle classifications influence a motor's efficiency and reliability is essential for optimal operation and minimizing issues.
1. **Grasping the Basics of Duty Cycles**: Understanding duty cycles is fundamental when assessing the operational limits of electric motors. It essentially describes the proportion of time a motor can operate at its full load capacity within a given timeframe, usually represented as a ratio. This concept is crucial for ensuring a motor's longevity and dependability in diverse applications.
2. **Decoding Duty Cycle Classifications**: Motors can be categorized into different duty cycle classifications – such as S1 (continuous operation), S2 (short-time operation), and S3 (intermittent periodic duty) – which provide insights into their intended use cases. This classification system has a direct influence on thermal behavior and the selection process for particular applications.
3. **Thermal Behavior and Duty Cycles**: An often-overlooked aspect of duty cycle labels is their effect on thermal management. Motors engineered for continuous duty (S1) handle heat dissipation differently compared to those used intermittently (S3). Mismatches between duty cycle rating and application can easily lead to overheating problems.
4. **The Importance of Cooling**: Many motors require supplementary cooling, especially under fluctuating loads or prolonged duty cycles. The cooling method employed – whether natural or forced – significantly influences the motor's ability to maintain efficiency and prevent thermal failures. However, it's important to note that duty cycle labels don't always include this information.
5. **Beyond Steady-State: Transient Performance**: Duty cycle labels don't encompass the transient performance of motors during startup or load transitions. These periods can subject the motor to significant stress, potentially impacting its operational lifespan. Engineers should meticulously consider these transient behaviors when integrating motors with varying duty cycle classifications into systems.
6. **The Perils of Mismatched Duty Cycles**: Selecting a motor with an unsuitable duty cycle can lead to premature failures or performance deficiencies. For instance, employing an intermittent duty motor in a continuous application might cause overheating. This emphasizes the critical role of aligning the duty cycle with the intended operational demands.
7. **Harmonizing with Regulatory Standards**: Unfortunately, duty cycle labels on motors might not always be consistent with international standards, resulting in inconsistencies in operational expectations. It's vital for engineers to be mindful of both local regulations and application requirements when interpreting duty cycle ratings to ensure both safety and operational efficiency.
8. **Clarity Issues with Duty Cycle Labels**: Many manufacturers produce duty cycle labels without adhering to standardized formats, potentially confusing end-users. Having a clear comprehension of labeling systems across various countries and manufacturers is critical for precise application and performance forecasting.
9. **From Label to Reality: Real-World Performance**: In real-world settings, many motors might not function according to their labeled duty cycles due to changing operational conditions or user errors. This deviation underscores the necessity of thorough performance testing under realistic conditions to validate the reliability and efficiency of the chosen motor.
10. **The Risk of Overworking a Motor**: Engineers need to be cautious when dealing with motors designated for short duty cycles. Sustained operation beyond specified limits can degrade the insulation and mechanical components of the motor. Post-usage evaluations are essential for ensuring long-term reliability in demanding applications.
Understanding Chinese-English Motor Labels A Guide to Common Manufacturing Text Patterns - Service Factor Numbers The Truth Behind Motor Load Capacity
When determining a motor's ability to handle different loads, understanding the service factor (SF) is critical for both performance and extending its lifespan. The SF is a multiplier that shows how much over its rated load a motor can temporarily handle without causing harm. A motor labeled as 10 horsepower with a service factor of 1.15 can handle short-term power spikes up to 11.5 hp. While this offers some flexibility, consistently exceeding the standard load can lead to reduced efficiency and a shorter lifespan. It's important that those working with motors regularly evaluate their load and efficiency to avoid prolonged operation outside the intended range. Understanding this concept is crucial for engineers and maintenance personnel when they choose and operate motors to prevent issues with overloading and diminished performance. This careful attention to detail minimizes the risk of problems and improves the effectiveness of the motor in an application.
1. **Understanding Service Factor:** The service factor (SF) of a motor is essentially a safety multiplier that tells us how much extra load a motor can handle for short periods without suffering damage. It's like a built-in buffer for unexpected surges in demand. For example, a 1.15 SF means a motor can briefly tolerate 15% more than its rated load. This ability to handle momentary overloads can be crucial for certain applications.
2. **Higher SF Doesn't Always Mean Better:** While a higher SF seems like a good thing, it's not always the best choice. If a motor operates consistently at or near its maximum SF, it may not be running at its peak efficiency, which can cause it to get overly hot and potentially shorten its operational life. It's a balancing act between capacity and efficiency.
3. **SF Varies Across Industries:** The needed SF can vary depending on the specific industry or application. For instance, refrigeration systems often utilize motors with higher SF ratings due to the frequent and sudden changes in load and the nature of the environment. This shows that the SF needs to fit the specific workload.
4. **A Safety Net:** The SF essentially serves as a built-in safety margin for motor operations. However, using a motor consistently at its maximum SF can lead to things like excessive heat and accelerated wear. This suggests that, in selection, we should aim for a motor that meets the required loads while still maintaining a reasonable buffer for safety.
5. **SF's Impact on Efficiency:** Running a motor at or beyond its SF can lead to reductions in its energy efficiency. That extra power being pushed into the motor isn't always being converted into useful work, which ultimately translates to increased energy costs. It's something to be mindful of when optimizing performance.
6. **Variability in SF Definitions:** Sadly, there isn't always a universally agreed-upon standard for how SF is defined or measured across different manufacturers. This lack of consistency can make comparing motors tricky and requires careful consideration of the exact specification for each motor when making decisions.
7. **Heat and SF:** The SF has a direct connection to how much heat a motor generates. If the motor is frequently overloaded, the temperatures can rise to dangerous levels which could eventually damage the motor's internal insulation or cause other issues related to reliability.
8. **Dealing with Changing Loads:** The SF is particularly important when a motor is subject to constantly changing loads, what we might call dynamic load conditions. Motors that are made to handle steady, unchanging loads might not fare well under the stress of frequently reaching their SF limit.
9. **Long-Term Impact of Overloads:** The repeated occurrence of overload conditions, even if they fall within the SF range, can cause a cumulative wear and tear on the motor's components. This highlights the importance of routinely inspecting motors and conducting maintenance to ensure long-term reliability, especially in harsh environments.
10. **Meeting Regulations:** In many parts of the world, there are regulations regarding the SF of motors, especially those used in industry. Understanding these requirements is essential to ensure that motor applications adhere to safety standards and prevent any legal issues stemming from operational risks.
Understanding Chinese-English Motor Labels A Guide to Common Manufacturing Text Patterns - Decoding Common Voltage and Current Specifications
This section delves into the crucial information found on motor nameplates, specifically focusing on voltage and current specifications. These details—operating voltage, full load current, and others—are fundamental for ensuring a motor functions correctly in its intended use. Understanding these ratings is key for engineers and technicians aiming for optimal performance, especially in demanding industrial scenarios where precise matching is paramount.
Interpreting these electrical ratings, however, is not always straightforward. The section touches upon the complexities involved and warns against making incorrect assumptions about motor capabilities. Misinterpretations can lead to inefficiencies and potential problems within the system. Overall, a grasp of this information is vital for anyone involved in choosing and implementing electric motors in various applications, ensuring compatibility and maximized performance.
When deciphering motor labels, especially those with a mix of Chinese and English, it's crucial to understand the voltage and current specifications. These seemingly simple numbers reveal a lot about a motor's capabilities and how it'll perform within a system.
One intriguing aspect is the frequent use of dual voltage ratings, like 230V/400V. This design allows for flexibility in applications, but it also necessitates careful attention when configuring a motor for a specific operating voltage. If the voltage isn't matched correctly, it can significantly impact motor efficiency.
The full-load current rating provides important clues about a motor's intended workload. Higher current ratings generally suggest the motor can handle larger loads or more demanding tasks, which can be beneficial but can also increase energy costs if not considered during design.
Voltage sags, which are temporary dips in voltage, can be problematic for motor performance. During a sag, the motor may need to draw more current to maintain its output power. This can lead to undesirable effects such as overheating or reduced efficiency. It's important for engineers to take power supply stability into account, especially when selecting motors for applications that are susceptible to power fluctuations.
In three-phase motors, current phase angles are crucial. Understanding the relationship between the current phases is essential for optimizing the motor's performance and efficiency. Incorrect phase alignment can introduce increased losses and even lead to potential damage over time.
Motor labels often overlook the power factor, a critical piece of information that shows how effectively a motor converts electrical energy into mechanical energy. A low power factor can be a sign that the motor is operating inefficiently and may indicate a need to explore better power management solutions.
Motors rated for higher voltages typically operate more efficiently as they draw less current for the same power output. But, this efficiency comes with a caveat. Higher voltages can introduce a greater risk of insulation failure if not properly managed within the system.
The nuances of RMS (root mean square) and average current values should also be carefully considered. While RMS current is frequently used to represent motor ratings, it's important to understand how it differs from average current. Confusion in this area can easily lead to faulty estimates of thermal performance and energy consumption.
Every motor has a brief but powerful surge when it starts up. This initial inrush current can reach five times the motor's rated current. Engineers must take this into account to prevent issues such as circuit breaker tripping or potential damage to sensitive electrical components.
When choosing a motor, it's important to be aware of whether it's designed for continuous or intermittent operation. These duty cycles impact both voltage and current specifications and can have major consequences on system design.
Finally, we need to address a somewhat frustrating aspect of motor labels—the inconsistencies between manufacturers. They might present voltage and current ratings in slightly different formats or use different standards. This means engineers need to be very careful when comparing motors from different sources to ensure proper compatibility and to avoid any misapplications within industrial settings.
Understanding the details of motor labels, especially those from Chinese manufacturers, can be a puzzle for those who aren't familiar with them. However, by paying careful attention to the voltage and current information provided, we can achieve better understanding of how these motors operate and use them more effectively.
More Posts from transcribethis.io: